
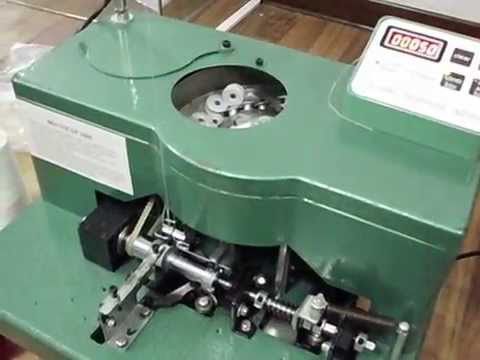
He begins by noting, as many others did at JEC, the “sustainability wave” that is washing over the composites industry. Thierry Merlot, Hexcel (Stamford, Conn., U.S.) president – Aerospace for Europe, MEA/AP & Industrial, sat down with CW at JEC to talk about carbon fiber and composites materials for established and emerging markets. Hexcel outlook on sustainability, hydrogen, AAM Cannon Afros reports that the Direct Infusion system can work with all the most common resin matrix. Cannon Afros says that the system is already used for blade production to infuse epoxy.
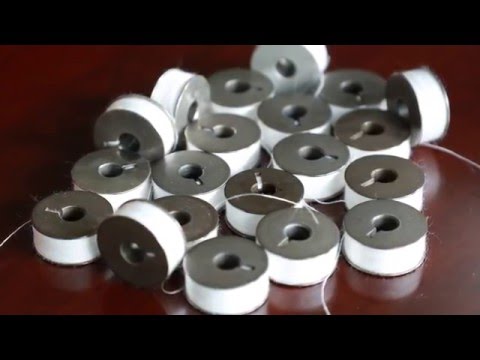
Further, the system allows resin injection to exploit the pressure given by the pumping system and not only by the mold vacuum, which expedites infusion. Cannon Afros says this enables precise control of resin injection at specified ratios, flowrates and pressures in strategic locations. For the wind energy market, Cannon Afros reported that it has provided a wind blade manufacturer with its newand enhanced Direct Infusion process. With this system, several infusion gates can be managed by the dosing and mixing machine, with each gate independently and directly controlled, but fed by the same dosing group. Cannon Ergos did the mold build, material characterization and trials were performed on a Cannon press using compression molding.
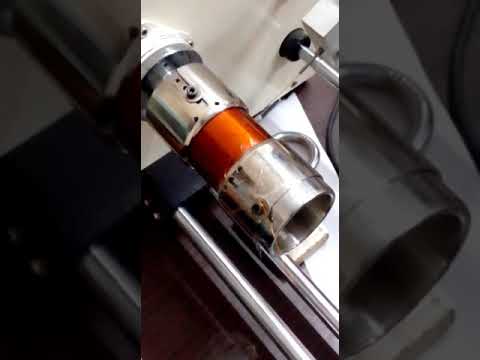
Photo Credit: Cannon Recycled carbon fiber thermoplastic 737 sidewall panel demonstratorĬannon Group revealed at JEC that its Cannon Ergos (Caronno Pertusella, Italy) unit has completed fabrication of a demonstrator 737 sidewall panel made with recycled carbon fiber and a thermoplastic resin system for Boeing (Chicago, Ill., U.S.). Roeffaers had on hand at the show several side-view mirrors made by CAC with flax fiber reinforcement. Emphasis is on helping automakers meet sustainability goals through use of renewable and CO 2-friendly materials. Michael Roeffaers, managing director of the operation, says CAC focuses heavily on fabrication carbon fiber composite parts, with natural fiber reinforcement offered/applied where possible, for automotive OEMs. Cobra’s automotive manufacturing operations, called Cobra Advanced Composites (CAC), employs 600 people in a 10,500-square-meter facility. In the medical market, Cobra is working with Chulalongkorn University in Thailand to develop carbon fiber foot prosthetics for people injured in motorcycle accidents. Cobra is also fabricating <10-meter wings for unmanned aircraft systems (UAS), as well as structures for mapping drones. This includes development of a wing for wing foiling and a windsurfing foil and fabrication of a recycled/recyclable surfboard, made with offcuts from Cobra’s automotive operations. Danu Chotikapanich, CEO of Cobra, says much of the company’s focus has been on electrification of outdoor products and development of foils for watersports structures.
